Modélisation du boitier
Objectif
Concevoir un boîtier sur mesure pour accueillir l’ensemble des composants électroniques, tout en s’adaptant aux contraintes physiques de l’écran, des capteurs et d’une fixation possible sur une tenue pompier.
Conception sur OnShape

Modèle sur OnShape – Vue globale
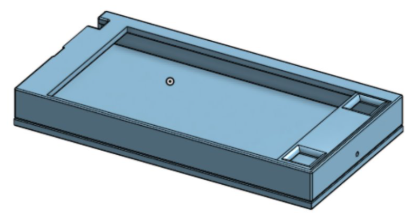
Modèle final prêt pour l'impression 3D
Étapes de prototypage
- 1er prototype – Découpeuse laser
Réalisé en bois fin. L’espace entre les boutons et les bords était trop réduit, rendant la structure fragile. L’épaisseur insuffisante provoquait des cassures à la manipulation. Ce test a permis d’identifier les zones à renforcer. - 2e prototype – Découpeuse laser
Découpe plus nette et épaisse, mais bord de l’écran et zones de bouton trop rigides. Le positionnement nécessitait des ajustements de profondeur. Nous avons alors intégré des congés et une courbure sur OnShape pour mieux épouser la forme des composants. - 3e prototype – Impression 3D (test d'ajustement)
Ce prototype a permis de valider l'ensemble des dimensions : écran, boutons, câblage. L'ajustement était bon et les composants s’inséraient correctement. Cela nous a permis de passer à la modélisation complète du boîtier. - 4e prototype – Impression 3D (boîtier final raté)
L’impression complète a échoué à cause d’un affaissement lors de l’impression des bords verticaux. Le résultat présentait des irrégularités bloquant l’insertion de l’écran. Cette erreur nous a permis de corriger les points faibles du modèle pour réussir la version finale.
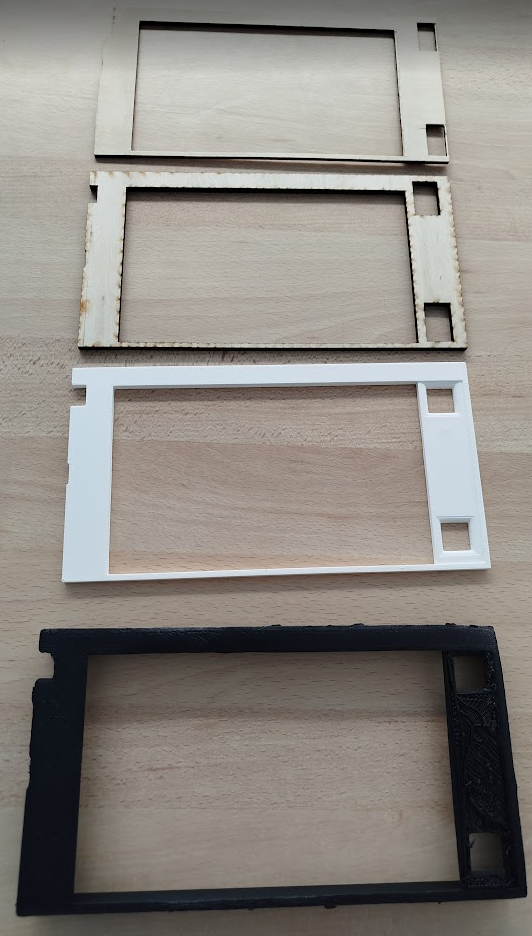
Maquettes testées (laser + 3D)
Résultat final
Le boîtier final, imprimé en PLA, s’ajuste parfaitement autour de l’écran tactile et des composants embarqués. Les inserts prévus n’ont finalement pas été nécessaires grâce à un système d’emboîtement précis et solide.
Le tout reste démontable, réutilisable, et prêt pour être fixé à une tenue de pompier dans une version ultérieure.

Prototype final assemblé
Cette modélisation offre une base fiable et réplicable pour une intégration future dans un boîtier certifié anti-feu.